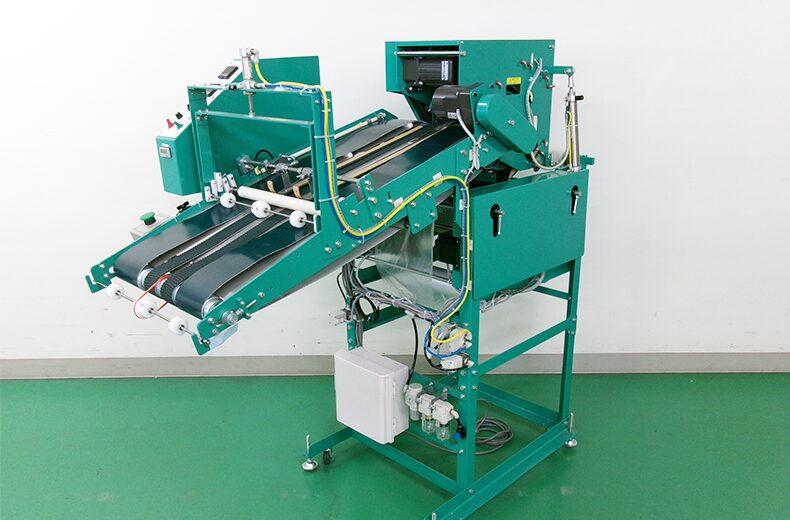
お客様の課題
H社様では、長年の協力会社である工場が職人技によって高品質な製品を製造していたものの、近年では職人の高齢化が進み、技術の継承や管理に課題が生じていました。
また、属人的な技術に頼る製造体制が続いていることで、技術力はあるものの作業の標準化が難しく、品質の安定や管理コストの増加に悩まれていました。
こうした背景から、今後は図面や品質管理の基盤がしっかり整った会社で、設計から製造までを一貫して対応できるパートナーを求めて、当社へご相談いただきました。
解決までの道のり
まず、H社様からいただいた図面をもとに、当社で2D図面と3D CADデータを新たに作成し、試作製作に着手しました。
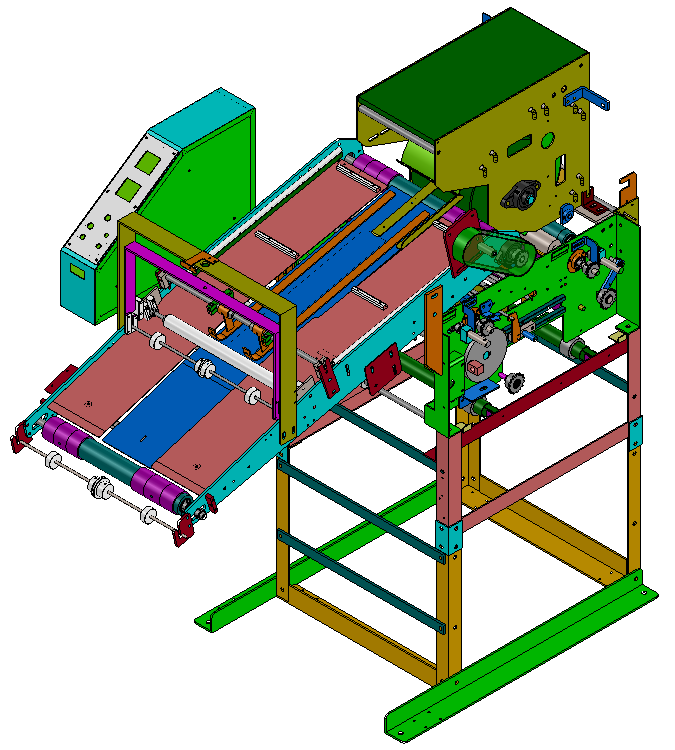
この段階で、元の図面と実際の製造現場との間で生じる不整合を精査し、必要な修正や更新を行いました。
また、量産に向けて効率的な生産と組立を目指し、部品の形状や配置を再検討。
具体的には、部品点数を減らすため、複数の板金部品を一体化する提案を行い、材料費や加工費の削減につながるコストダウン仕様を実現しました。
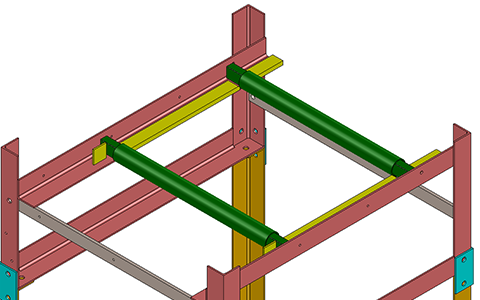
部品形状の変更前
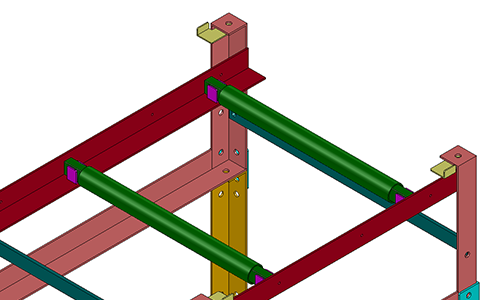
部品形状の変更後
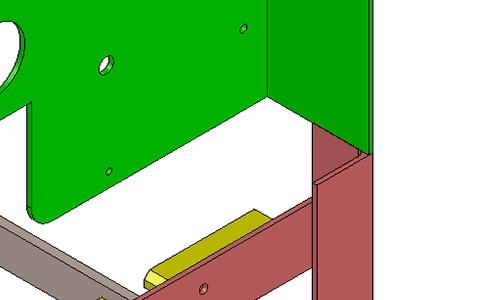
ボルト締め変更前
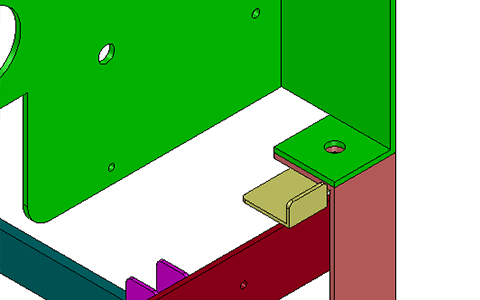
ボルト締め変更後
こうした工夫により、製造や組立の効率が向上し、全体のコスト削減と管理工数の軽減を達成しました。
また、図面の修正を行うだけでなく、長期的に安定した品質を確保するための図面管理や生産管理体制についてもサポート。
設計から生産までを一貫して担うことで、工程管理や納期管理の面での安心感を提供しました。
完成までの工程
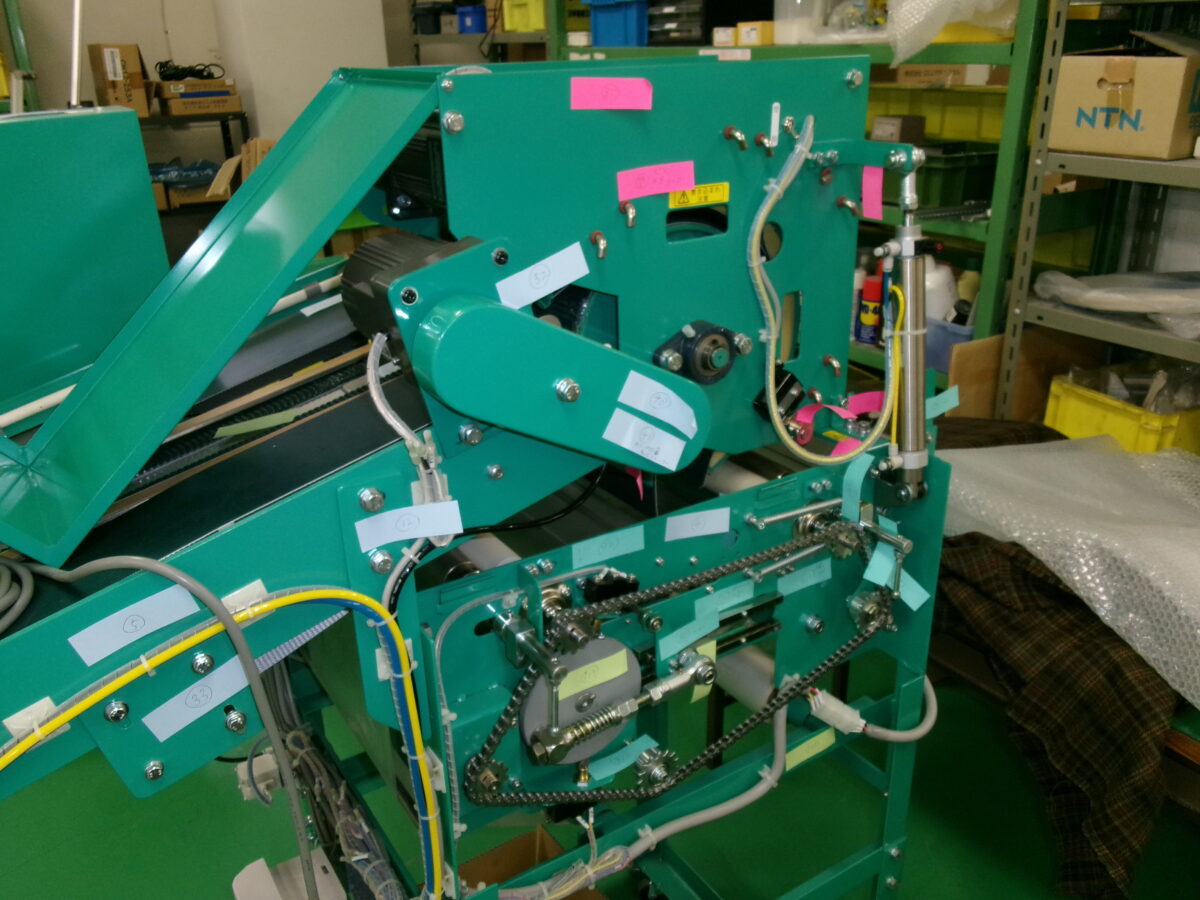
1. サンプルから構成パーツの洗い出し
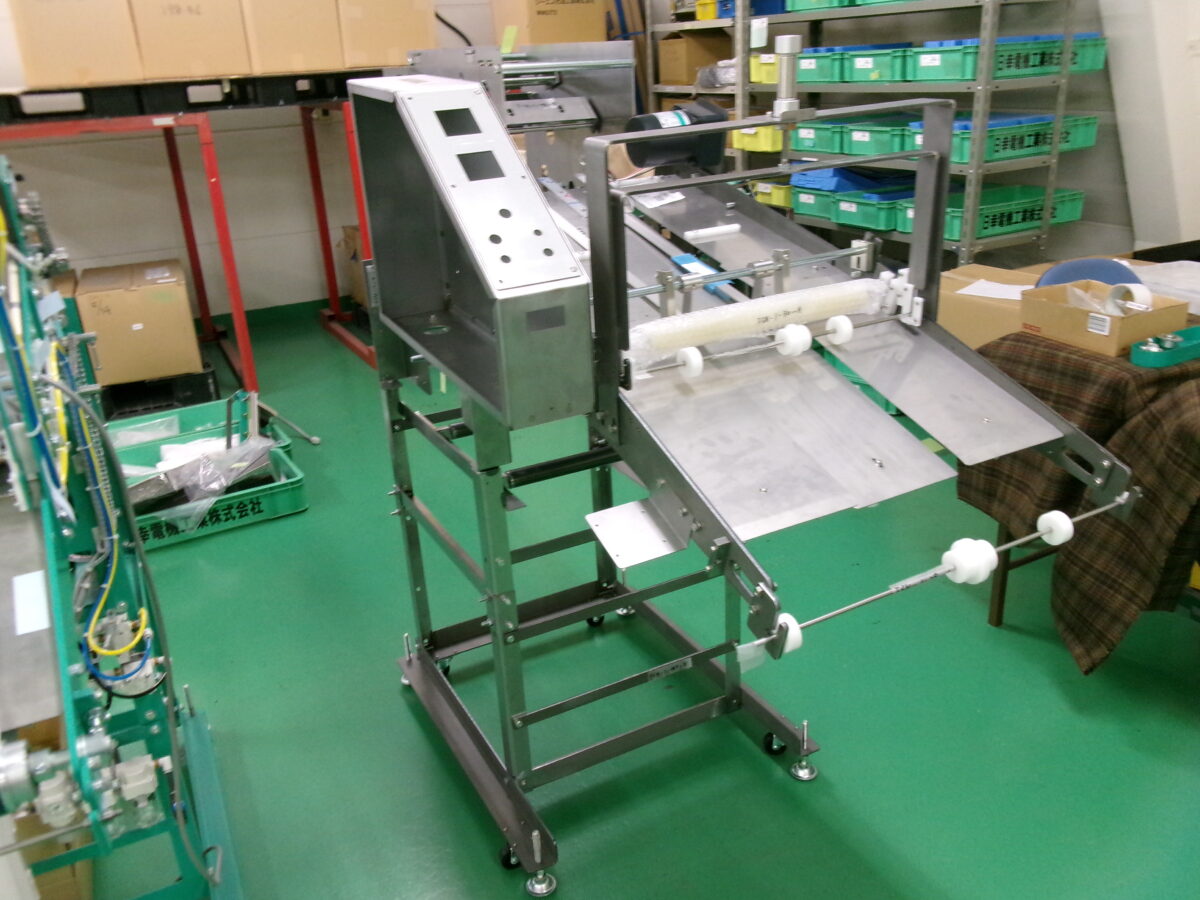
2. 仮組み
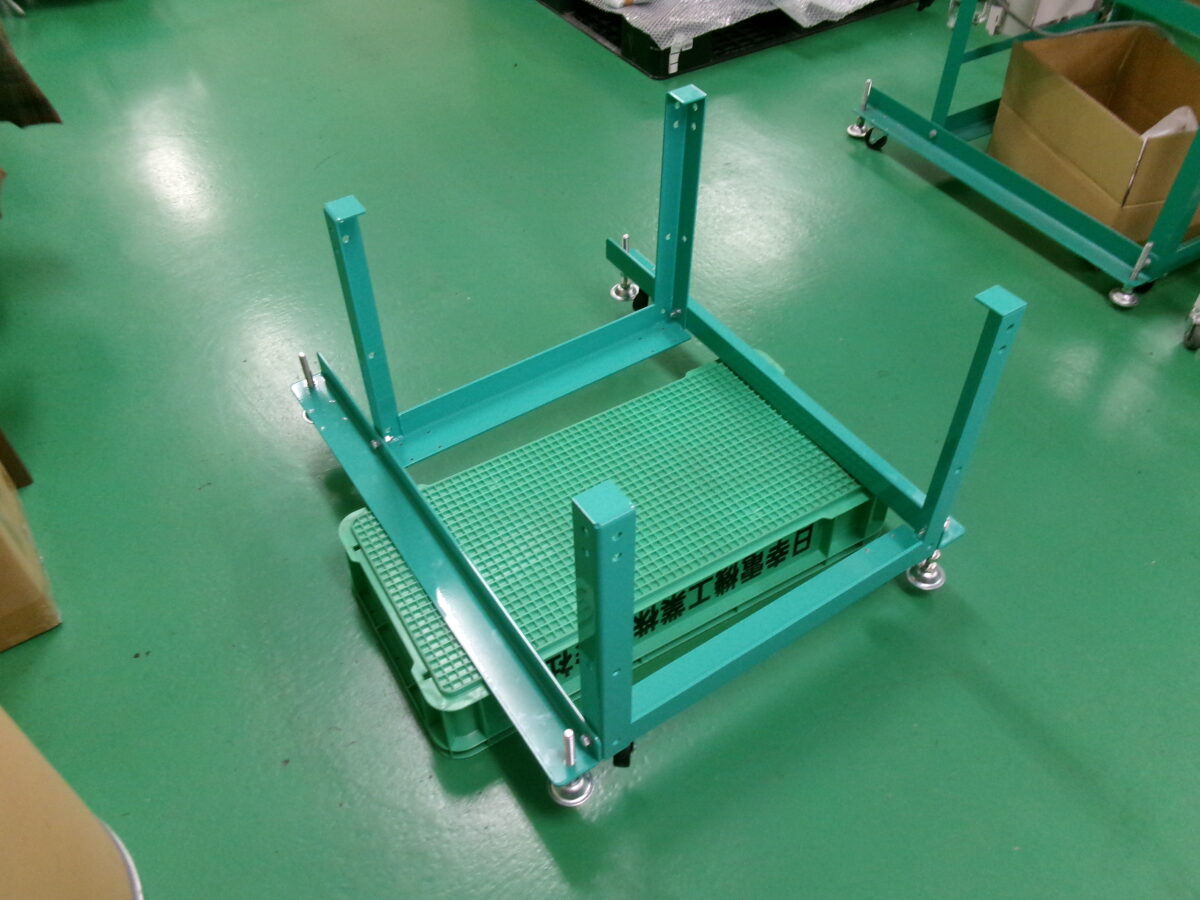
3. 塗装後の確認とフレーム組立
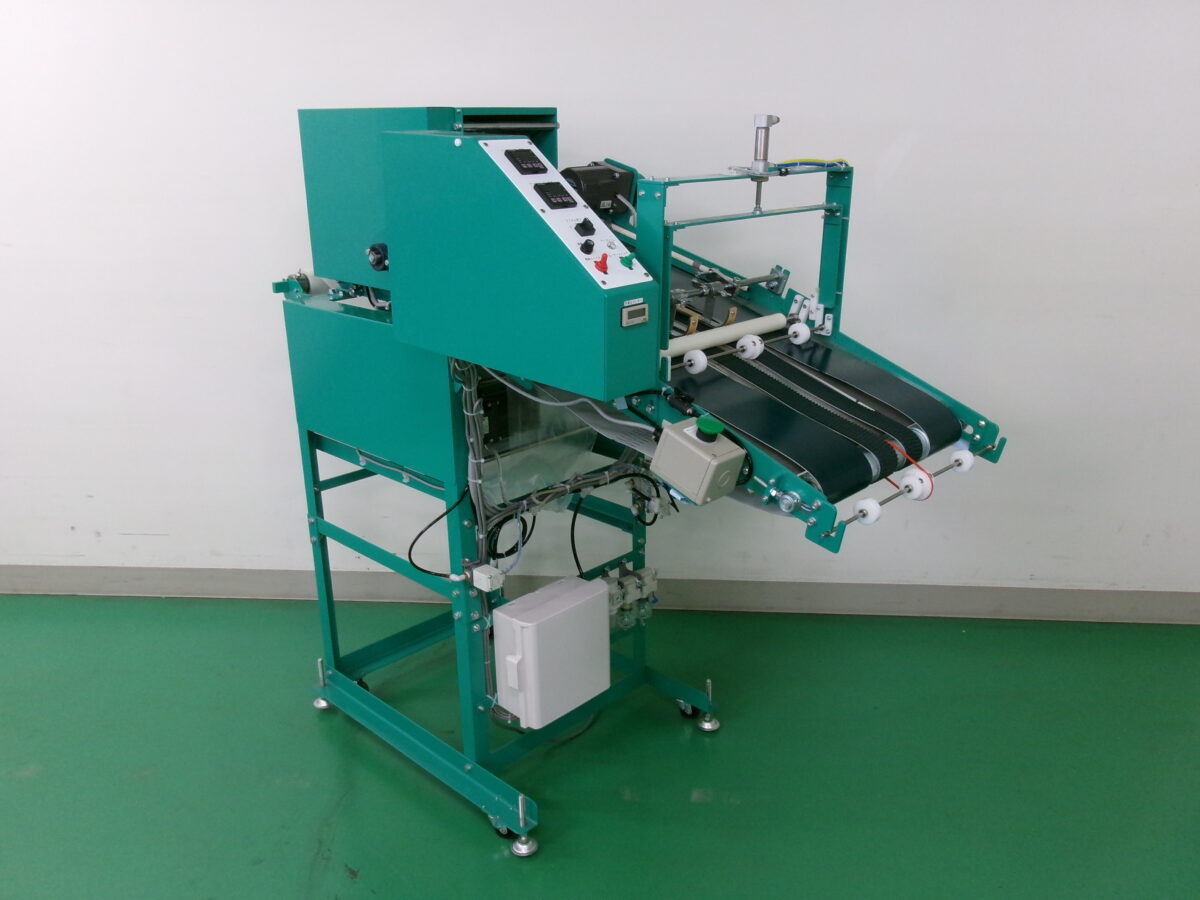
4. おしぼり梱包機の完成形
課題解決の結果
試作品が完成し、H社様の現場にて数か月にわたる試験運転が実施されました。
現場からは、スムーズな稼働と特に問題のない仕上がりについて高評価をいただき、正式に量産体制への移行準備が進んでいます。
この一連の取り組みによって、H社様は属人化からの脱却と効率化を実現し、今後の事業拡大に向けた生産基盤の整備に成功しました。
今後も継続的に技術サポートを行い、信頼できるパートナーとして品質向上と安定供給を支援してまいります。